VLOG!!!
Hey guys, this is MarbleGenius149 Tube and today this will be my first vlog.
Yeah, that's right. Vlog.
Now, first of all, I have some things to say.
one,
I am so sorry for not being active on my gaming account.
No really. No really, really, really, really.
I am so sorry for not being active on my gaming account.
but, I will be back on Monday and Wednesday, so stay tuned on what games I will be doing.
Oh, and also 2,
I am planning on my Hot Wheels and Marble machines.
as you can see, it's work in progress.
I know!
Anyways, number 3,
I got a copyright strike.
No, seriously, no seriously, I seriously got a copyright strike.
but don't worry! My copyright strike will expire on 2 weeks.
yeah that's right 2 weeks, because
I contacted the claimant Robert Samson, yeah that's right, Robert Samson,
he told me, that he will retract my copyright strike within 2 weeks.
I know, right?
So, that's it! If you have any questions for me, and I will be answering them as soon as possible.
Peace out, people!
For more infomation >> MG149Vlog - Episode 1 - Duration: 2:02.-------------------------------------------
Pokeland Legends: How to unlock the 4th and 5th Passive Skill Slots of a Pokemon - Duration: 10:09.
HELP THIS CHANNEL IMPROVE! SUBSCRIBE FOR MORE VIDEOS!
HELP THIS CHANNEL IMPROVE! SUBSCRIBE FOR MORE VIDEOS!
-------------------------------------------
ll Orange and lemon granita ll Bakery_channel ll - Duration: 1:52.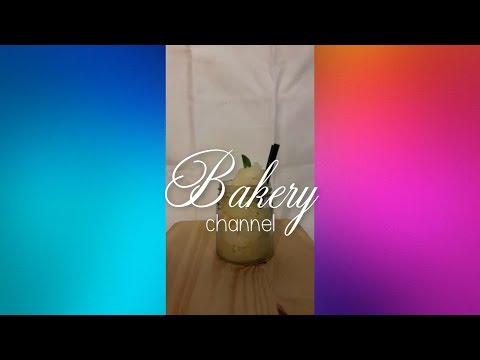
-------------------------------------------
Передаю приветы в следущем видео !!) - Duration: 0:43.
-------------------------------------------
Question answer! - 2k17 - Duration: 6:18.
Бля
Бля
Бля
Бля
Бля
Бля
Бля
Бля
Бля
Бля
Бля
Бля
Бля
Бля
Бля
Бля
Бля
Блч
Бля
Бля
Бля
Бля
Бля
Бля
Бля
Бля
Бля
Бля
Бля
Бля
Бля
Бля
Бля
Бля
Бля
м
Бля
-------------------------------------------
Please, don't touch enything #2 | 2 zakończenia które musisz zobaczyć! - Duration: 10:10.
-------------------------------------------
My channel intro - Duration: 0:11.
plz kill me
I want to die
-------------------------------------------
DEPRESSING RAP music animation - Visualization of SAD RAP INSTRUMENTAL music - Duration: 2:19.
Depressing rap music animation for you! Sad rap instrumental.
Sad, even tragic, high-pitched hip-hop beat in a modern style. Mesmerizing and makes you wonder.
Interesting track. It is visualization of hiphop beat, something like lyrical rap.
"Take A Ride", composer Andreas Jamsheree, depressing rap.
Turn off the light and if you like instrumental rap -
enjoy this audio animation effects of instrumental music, hip hop r&b vj visuals!
Beat-map technology for sad hip hop beat! Processing particular special effects, optical flares of music.
So go on, music animation video of sad rap beat! This is love rap beat.
-------------------------------------------
MY PET RAT! - Duration: 3:05.
"Hey I know a game we can play!"
"I'm not playing any game its 27 degrees out!"
"It don't matter if its 3 degrees or 300 degrees were playing this game!"
"Alright fine what is it"
"So I kick this ball and you have to get it!"
"You know that sounds really bori... PLAY IT!"
"Ok here I go"
"Haha now you have to go get it!"
"Alright fine"
"Going to get the ball!" x3
"Wheres the ball?"
"Do you mine if we get the ball back?"
"AH don't eat me!"
"I see you just want to have fun!"
"If you want to come you can follow me!"
"You are going to be my new pet!"
*Friend Song*
"Know was today fun?"
"Petter?
"Where did you go?"
"Calm down what did I do?"
"Oh."
*Halloween Theme Music*
"You smell pretty good!"
"Have you been using my deodorant?"
"What a horrible dream!"
"OH NO!"
-------------------------------------------
Welcome to My Channel - Duration: 1:55.
Hey Guys
welcome to my channel
in my channel i make movies ,series and a bunch of other
By subscribing and liking my videos.
that just tells me to make more!
i will also be puting polls and questions on what you guys want me to do next!
-------------------------------------------
SHOUT OUT SUNDAY #1 | Joe the Fedora Gamer - Duration: 1:52.
Music : Forward Thinker - Silent Partner
Music : Forward Thinker - Silent Partner
Thanks for watching!
Like, comment, and subscribe for more!
Follow me on Facebook, Twitter, and other social media.
See you next time!
-------------------------------------------
Welcome to My Channel! - Duration: 1:05.
Hello everyone! My name is Ethan The Dinosaur Kid,
and welcome to my channel!
Uh, yeah! (Silence =I) Um, my channel will be mostly about gaming
and analysis videos, MOSTLY! But, yeah!
And tutorial videos to! So yeah! This channel will be
a great channel! =D I will do a lot of
fun stuffz! That you guys like!
Like a lot of games like 'Slime Rancher',
Or 'Five Nights at Freddy's' or Jurassic Park (Operation Genesis)
I mean we have to play every single dinosaur game
that is the GOAL of this
CHANNEL!! sOOOOOO, (More silence) yeah, this was just a little
introduction video to uh let you guys
know about my channels and YEAH! =D So,
I shall see you guys during my channel! ( Ethan, you said 'channel' enough) BU BYE!!
-------------------------------------------
It's a Vegas Family Contest!!!☺😀 - Duration: 1:36.
It's contest time!
Always look at the Brightside!
I am so excited!
Rule #1 Subscribe to both of our channels- VegasFamilyFunTimeTv and The Brightsides Family.
There will be a link below.
Rule #2 Leave a comment on any of our videos starting now until midnight Friday the 3rd.
Every comment is an entry!
That is all!
We will use Random.org to help pick 1 lucky winner.
Here is what 1 lucky winner will get...
We will give you a special shout-out in our video.
And add you to our channel description box as our top "Brightsider" for 1 whole month.
Then we are going to Skype with you for 15 minutes from right there.
That is where we are going to Skype from for 15 minutes.
From a famous Las Vegas Landmark!
We are so excited to talk to 1 of you!
Bye!
-------------------------------------------
[VIETSUB] BTS dẩy đầm đón năm mới - BANGTAN BOMB BTS stage greeting the New Year - Duration: 7:52.
-------------------------------------------
Welcome To My Channel!!!!! - Duration: 6:32.
YA!
I keep It Goin!
CHANNEL
(there goes me singing XD)
-------------------------------------------
We Need to Kill Our Perfectionism! - Duration: 1:48.
Oh I kind of want to see my notes.
I should just like talk naturally about it and then grab the best sound bytes from it.
Hey guy!
I don't know how to start these things.
Alright, alright, alright, alright, alright, alright, alright, My name is Zach Sperrazzo
and I'm a filmmaker and umm... no see I keep like-
I hope you enjoy my channel.
So my goal for this channel is to make stuff so that I can consistently create stuff, stop
saying stuff.
Hey guy!
I'm desperate follow me!
That's horrible, ok I don't like that at all.
My name is Zach Sperrazzo....
See I feel expressionless because I'm overthinking everything I'm saying.
SO!
Do I look expressionless when I'm talking to the camera?
A little bit.
Really?
Bummer, okay here we go.
Hey!
What?? it's so weird.
Alright long story short umm, subscribe.
Just kidding.
Do good a lot! okay here we go.
-------------------------------------------
El puente de la muerte__impresionante!!! - Duration: 2:59.
-------------------------------------------
Large Format 3D Printer Episode 10 - Actual Progress!!! - Duration: 4:00.
whats up youtube it's patrick with Nolan C 3d
print works and we're back with episode
10 of the large-format 3d printer build
and as you can see just by this pile
of parts we ran into a few problems but
I'll get more into that as we move into
the video in the previous video we
resolve some of the top of the access
amount issues with that taking care of
it was really time to get this frame
bolted together started with the sides
and right from the beginning the frame
slot me I don't have a drill press and
the possibility of getting a hole
drilled moderately straight from one
side of the aluminum to the other well
it's about 5050 after having a machine
gun effect start to appear on my
aluminum and then I snapped a drill bit
i decided it was time to give the dremel
shot i install the router adapter but
left the set screw loose for the journal
could act like a drill press giving me a
bit better chance of shooting straight
holes from both sides of the tubing
as you can see the whole turned out much
better and less of that machine gun
effect you may remember back in episode
6 I had to replace a broken corner break
the red ones take about eight hours to
print side reduce them down to just
corner inserts like the white one shown
here these reprints turned out to be a
major benefit as it made installing the
pulley bracket so much easier here in
the front where the motor mounts are
i'll have to remove some of the outside
shroud to allow for the motor install
and general function after all this I
started putting the frame together
including putting and those fronts
latitude and here it is the frame all
bolted together now it's time to work on
the z axis we headed outside to break
out the grinder and cut the linear raj
from mcmaster carr i used the standard
cutting disc in my grinder i marked my
measurements of 48 inches and checked
them twice before starting my cut I have
to say that's had me nervous
I mean one mistake and I was going to be
paying for it once cut switch back to a
grinding disc and rounded the edges
slightly this removed any burning and
age in the installation my next step was
to assemble the entire the axis however
I found another issue back in episode 7i
six-hole alignment for the top of the
excess amount in relation to the bottom
motor mount but I'd failed to fix it on
the sliding bed mount and you can see
here it's just slightly off i fix the
problem in teacher cad and printed the
new ones in ABS clean them all up and
started the install now use my level to
get the access of the line as possible
I claim the bottom motor mount to the
frame to ensure wouldn't move while I
was drilling holes the next issue was
how to bolt up the top mount originally
I was going to go through the side
doing so would mess with the sliding of
the linear rails so i had to switch over
to going top to bottom here you can see
i added some voids and some hole size
just right to the bolts amusing and I
reprinted these parts as well using abs
so here the completed z-axis the first
side ended up being more trial and error
with the second side going together a
bit smoother
well that about does it for this week
we'll see what happens next week when we
take it apart and move it back out so
it's more permanent home in the back
shed
if you guys are looking for some other
large format builds let me go ahead and
point out two channels out there first
of the print 3d channel Jeffries doing a
project called 3dp 365project printing a
different model every day on his gmax
1.5 xt plus another channel is Ivan
Miranda he has a great build in progress
and i really like his clamping setup
links to both of these channels will be
down in the description if you liked the
video give it a thumbs up or thumbs down
it's your choice remember if you want to
see more content on this build or be
notified when we put out a new video be
sure to hit that subscribe button and as
always thank you for watching
Không có nhận xét nào:
Đăng nhận xét