HRH Prince Andrew meets Commonwealth Games volunteers at Gold Coast Sport and Leisure Centre, Carrara.
Duke of York Prince Andrew reveals British Royals will visit Commonwealth Games
His Royal Highness the Duke of York told one GOLDOC employee a number of "very important people" would visit the Coast during next year's Commonwealth Games.
Taleah Kneebone, 25, who will be working in the Games Village and greeting VIPs, met the Prince at the Gold Coast Sports and Leisure Centre at Carrara on Saturday.
HRH Prince Andrew meets badminton players at Gold Coast Sport and Leisure Centre, Carrara. Picture: SuppliedSource:Gold Coast Bulletin.
"He was so human, I can't stop smiling every time I think about it, it was actually one of the highlights of my life," she said.
"He told us that when Royals go to the Games, it's the volunteers who are the 'cream on top' that really make or break the event.
HRH Prince Andrew visits Currumbin Wildlife Sanctuary. Picture: SuppliedSource:Gold Coast Bulletin. "He said we'll have some very important people coming through next year and that we will be greeting some members of his family at the Commonwealth Games.
A number of security guards from the Palace kept a watchful eye over Prince Andrew, who was accompanied by a convoy of police and Royal aides.
For more infomation >> (News)Duke of York Prince Andrew reveals British Royals will visit Commonwealth Games - Duration: 1:43.-------------------------------------------
WHO WILL WIN! (use subtitles) |Impossible Creatures Multiplayer - Duration: 5:13.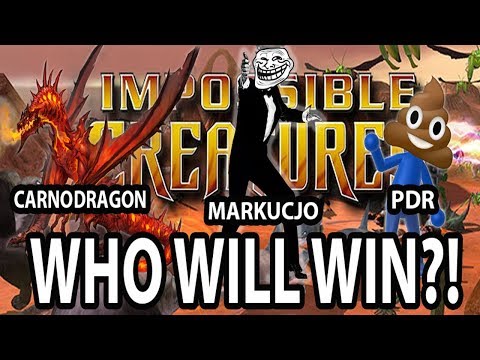
*Hey! Thanks for watching!*
Alright, new game! Multiplayer.
Uh, this is Mark (Markucjo)'s character, guy, icon.
I was supposed to do an MLG edit and then it just ended up like this. I still like It though. I don't care.
This is what I imagine Carno (CarnoDragon) to look like (He's not even human, just a dragon.) and then there was also me!
Literally me every game.
Like, 'go!'
I agree.
Alright, so this is just me showing off my base uhhh.
I don't know. What the heck did I do wrong? (Everything :'( )
Like, I feel like I focused too much on like the sound beam tower things.
They're really only useful for like the beginning of the game, but I don't know, man.
Uh.
Looks cool though, still.
All peaceful like.
Got all the coal.
Yep.
And, then everything starts going to shit.
So sad.
Is there a way to, like, convert electricity to coal
faster, because like otherwise, I'm gonna get carpal tunnel. I really don't want that. Like, I pressed that button so many times, it's ridiculous.
Uh. I think this is Mark destroying me right now. Like, I don't stand a chance. Oh my god.
I gotta make my own army.
Geez.
I mean look, there I go spamming again. Carpal Tunnel.
Get a brace or something.
Yeah, I don't know.
Not going well.
Yea, this the part where I tried to, like, create a few creature chambers
to like, yea, head him off right there. See if I can produce enough, fast enough.
No.
It's not going to work.
So sad. Yeah.
And, yup my base is gone.
Tragic.
Aaawww.
I felt so stupid.
Well, I'm good. I, I think I did an OK start, but look at how much he controls though. Look at this mess.
I guess what I should have gone for was that middle island.
Like, I don't know why I didn't.
Cause I saw it and I was like, 'Whoever gets that is gonna win!' and then I just didn't get it. Like look at this.
This is what you want.
But I was like, 'Oh, I can just rely on electricity, but I forget, you know, Carpal Tunnel and then I get bored of uh pressing the button.
So, you know.
Yeah. Carno put up a really good fight though. Like, It's crazy.
But, there's nothing you can do when somebody owns like majority of the map.
*leg slapping to the song*
What's that?
Oh, more [creatures].
Oh look at this helicopter. How- I didn't even know helicopters could do that.
That's ridiculous.
And, this lab defense thing is just like a giant F you. Like, 'Nah, I don't care. I don't care. You're not killing my base, yet.'
He (Carno) doesn't have anything else coming, I don't think, at this point. But, yeah he's (Mark) just, like, dropping in, like, his people. It's ridiculous.
Yep.
Like, 'Nope. Fuck you. You're not taking my base.
Okay, well okay. He's (Carno) gonna try to. I mean, I don't know. I would've just given up. I don't know. I give up to easily, maybe.
Carno [I meant Mark.] like, he just dropped 'em [his creatures] like, 'eh, whatever.'
Like, 'Nice try.'
But, I saw in one game that-
Yea, you can actually see it in the map in the uh
top, left corner.
He [Mark] has a water chamber all the way out there. Oh look at my comment. I just- I had to say it. Like, that's a ridiculous
helicopter. But, you see he [Mark] has a Water Chamber right out there.
But, that's the only way that you'd be able to, like, do this [be able to defeat someone when you're base is under attack like Carno's.]. And, survive, maybe.
But, yeah. It was a good game!
*clap*
*humming to song*
-------------------------------------------
Local farmer will meet with President Trump - Duration: 2:25.
-------------------------------------------
DCYF will not investigate Providence school employees - Duration: 0:20.
-------------------------------------------
Planet x Nibiru update 27th September 2017!!! BILLIONS PEOPLE WILL SEE NIBIRU IN THE HEAVENS - Duration: 32:57.
-------------------------------------------
Trump says he will 'fix the mess' of North Korea - Duration: 0:55.
-------------------------------------------
মুকুল রায় কি তাহলে এরপরে বিজেপি তে ? || mukul Roy will join BJP ? - Duration: 0:41.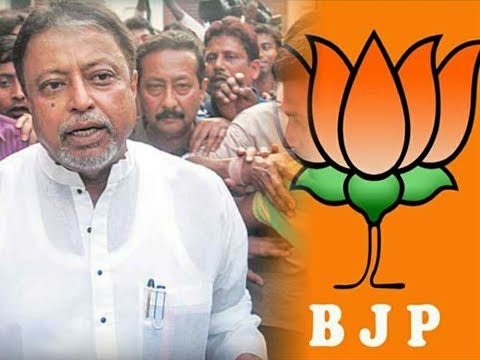
-------------------------------------------
Where will the new middle school be built? - Duration: 1:10.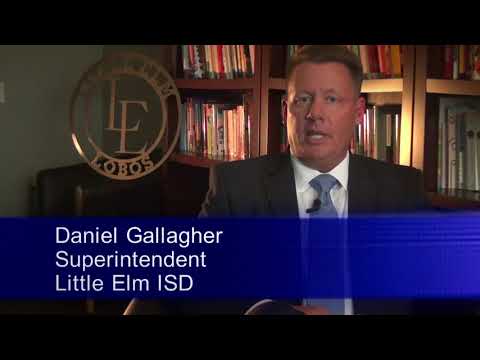
- My name is Lindsey Reyes, my husband and I
have lived in Little Elm for nine years.
We have two children, Matthew is in sixth grade
at Powell, and Max is in third grade at Brent.
My question to you is, where will the new middle
school be built and what is the timeline
of all the projects?
- The district is currently looking at all
options of where to build the second middle school.
When considering the purchase of land
and the construction of a new campus,
it's very important to look at demographic
trends so it's in the best location,
not just for 2017 but for decades to come.
The long range planning facilities committee
was comprised of 35 community members
who looked at our demographics trends
financial data, campus and district needs,
and Bond need scenarios.
All of the projects in this Bond proposal,
were recommended by this committee who prioritized
the projects to address student growth first,
if approved by voters, the district will establish
a Bond-oversight committee made up of parents,
community members, and teachers to help
guide the decision making process.
For additional information please
visit our Bond website at Little Elm ISD Bond dot net.
-------------------------------------------
Unique Visit to Record Industry: the Bach Partitas will be pressed here! - Duration: 25:45.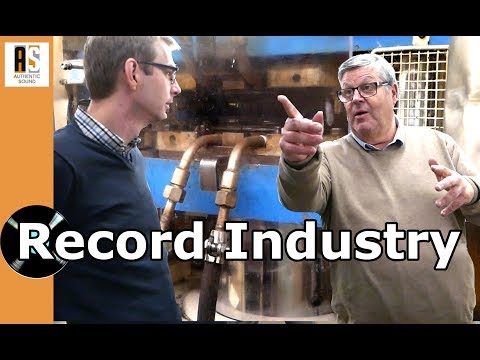
What's up everybody, welcome to this channel
that is all about exploring the music from Bach to Beethoven
and beyond, and sharing that with you
through performances and research, hopefully to inspire you on your journey
as a musician or as a listener
and today, this is a video I have been waiting for ages
to launch and to upload and to give it to you
because it is a very exciting subject
Anja and I went to Record Industry
where they make vinyl records
for a very long time, since, may be even
1950, in any case way back
They are probably the biggest pressing plant in the world
producing over a 50.000 vinyl discs
a day and the production is only increasing
So why did we go there?
You might remember that
I recorded all the Bach Partitas here on my clavichord
for YouTube, but I rerecorded them
on analog taperecorder
on our big Studer taperecorder to launch them as
a vinyl box, something perhaps, like this
So, we are working on that and of course, one of
the things that need to be done is to visit
a pressing plant where the vinyl discs are being produced
and of that visit, we made
a compilation. So in two words,
why producing, in this digital age, an analog recording?
Why record it on tape? Why release in on vinyl?
Well, there is a sound quality aspect to that
not going into this deep now
I will cover that in future videos, because I think it is important
What this Studer Taperecorder does with the sound
you can not imagine, it is like going back
to a world full of very relaxed
blending together sound
with an open stereo image that even
the high quality digital gear that we have here are not capable
of giving. Just not. And the vinyl discs
that, of course, is coming very close to that
analog sound 'feel', but more than that
I love the slowing down feature of it
You put a record on a turntable, you sit down
you light a candle, you drink a glass of wine
or beer, or whatever you like and you are
captured, you are the prisoner of that recording
it just runs, and it is very nice
not only to listen to, but to look as well
because it's turning
And in one way or another, I believe in this slowing down
feature, combined with the analog
audio quality aspect
because I can guarantee you, once you returned
or once you discover, depending on your age
the vinyl disc, the analog recording, it will be hard
to return to digital media
I am a 100 percent pro digital
But there are moments in live where
you just need something else, and that is the analog
recording, that is the vinyl production
that'll come in a very beautiful box
with a book, with four discs and
everything, also the CDs of course
that is for the coming months to be launched
but now I'm giving you that compilation of the
visit that we paid to Record Industry
in Haarlem, in The Netherlands
I will be talking in Dutch with the person who
is guiding us (Rinus Hoonigh), the master sound engineer
for Record Industry
We'll subtitle it from time to time (it's all been subtitled :-)
when I think it's important or just intersting for you to understand
so click on the closed captions
on your desktop or in the right hand upper corner
of your mobile device
to enable closed captions in English
and you see from time to time some translation (= always...)
Hope you enjoy this, leave me in the comment boxes
what you think about this project, what you would suggest
and what your
experience is with analog recording
with vinyl recordings, and how you see the future of that
would be great to read that
If this is the first time here, and than I'll leave you with the people in Haarlem
and with myself, on the video obviously
would love to have you subscribed
and join the Authentic Sound Community
because also sound, is something, recorded sound
we can explore here
and it is so
interesting to explore the world of recorded sound
as well. So, great to have you here
and up to Haarlem and see you later again!
Now we're going to the cutting rooms
Now, if I do the premastering for customers
when the premastering is ready
then the file is being cut here
and a in case of a digital file, the music runs
through the amps to the cutter
you are familier with a cutter? yes?
Well then you know how it works.
Two signals go to the cutter, one direct, one with a delay
and that delay is one period
If you're cutting pop music and this kind of drum sound
if you would not have this drum, the cutter does not have to move, but if suddenly there would be a loud drum sound
that'll create a high amplitude, which he needs to know one period in advance
It's being programmed in advance
So that the cutter can make space to allow that sound on the disc
And that is repeated all the time
For that it is called a one-to-one registration
So if you have a dynamic program
this still could allow you to have 32 minutes on one side
but on the very silent passages, the cutter can place the groves very close to each other
and for the expansions, he'll give room
And that is also the dynamic you see visually on the disc
We're now in one of the two rooms where we cut the lackers. Here we'll find the cupper plates, DMM.
When the Cd came in 1981
I'll have to make sure to be on par with the digital age
The higher frequencies on CD's
So, Neumann rebuilt a lacker table to a DMM table
so with other amps and different cutters
hence the name: Direct metal Mastering
This is a plate with a layer of cupper
And like you cut in lacker, you can cut in cupper with a diamond
Advantage is you'll have less inner grove distortion
You'll have more distortion at the inner side than on the outer side
It means that the more you go to the middle, the more kind of compression you'll have
you get a kind of natural compression
you'll notice as well a reduction of higher frequencies on the lacker
A lacker of course is soft material
it is a kind of plastic, so if you cut in that material
it rebounces a little bit
And just those very fine elements, like high sounds, there you'll notice a slight reduction
Well, the advantage of this is, that when you'll cut it with a diamond, it will not rebounce!
So your high frequency response is better
It'll be interesting to test your recordings with this
to see what suits your clavichord sound best, cupper or lacker
And of course there is a number, because you'll not be able to tell, other than the number of tracks, what music it contains
Here is a bit of distortion, here is some low, but if it is Michael Jackson is, I cannot see
So this is the disc that is being preserved?
yes
Another advantage of the cupper is that you are able to immediately make a mold
So you'll produce a negative that you can press from
On a lacker
That needs a galvanic bath
so to give the plastic electrical guidance
so the plastic is being covered with a layer of nickel
so it will have to go in a bath to cover it with silver
But the first one is not usable
so you'll have to take three steps
which gives a tiny bit of loss to the original
So here you'll have a laquer that has been in a bath that'll give this a tiny tiny layer of silver
now, silver conducts electricity
so this can go into a bath that'll give it a layer of nickel
that'll give you a positive and a negative
and with the negative you could start the pressing
but you can only do it once
a cupper disc is reusable
but from this laquer is only to be used once
so if you do that, you would have to cut a new laquer
for that reason, from the first copy is a new copy produced
the first goes into the archive
and from the second copy there will be produced metal molds. That is stronger and can be used up to 20 times
After that, the copy serves to make new ones
the first baths where the lacker receives its layer of silver
Let me open it for you
Here are the nickel particles
and the nickel will dissolve in small molecular particles
and because there is electricity run through it, those molecular particles will adhere on the silver coating
and after 40 minutes, we'll have 180 gram of nickel on the disc, which is enough
then we turn the machine off and we're going to separate the two discs
so we'll have the original lacquer with silver and the first 'father'
and the 'father' will be copied into the first 'mother'
that'll go to the presses
So the DMM procedure is a huge time saver, right?
yes, but it has to serve its purpose, it must be the right choice
For pop music it works nice, other music as well
but not all people like the sound of DMM since it has a kind of 'metalic' sound
There is only one way to find out, and that is trying both procedures
we have to innovate all the time. These are the last 'old' machines
almost all have been replaces by new ones, here is the latest we added
We have to, since we get more and more orders
If possible we built the machines ourselves. We still have some people who worked at Sony, CBS even
So this hall contain only baths, to get the orders produced we get
Centering a disc is very important, crucial even
certainly with an instrument as a clavichord, if you'd have long tones
and the discs would be a fraction out of center, you'd hear that immediately
So, these are two machines to center
What happens here is, that when the cutter makes the disc, he produces a round
and that circle is what here will be looked for with a light
and if the lights really stands still
then you'll know the whole is exactly in the middle
let's see if we can visualise the process
We're lucky!
In that machine, the discs is being sanded, with four different grains
the surface needs to be perfectly flat
that is the device to center
Now he will search for that ending (the exit) left by the cutter
And now the light will tell him were the exact middle is
So this is a matrix already, that'll be used for pressing
So and here you'll have the whole of which we know for sure is is perfectly centered
then it goes in the die-cutter
An easy way to see it is a matrix, is reading the number, it's printed in negative
the artisan aspect is what makes it the more attractive
Labels!
The old Columbia
orange
labels are printed here in house
A label is a difficult object to make
The press is 150° Celcius, but the paper should not burn, so the paper is of a special kind
The ink should not bleed, which could happen because of the temperature
So you'll need special paper and special ink
But even then it still can happen that the heat has an effect you don't want
That is why we take a pile of lables
they go in this machine
this is an oven with hot air of 150°C
It'll affect the labels
a kind of enamelling
The advantage of this procedure is, that once through this machine, it will never cause problems while pressing
And there you'll have the boxes where they wait to be used
And this is the pressing hall
So now the machine enters a 'little bread' of vinyl with the labels
the spacer is important, since the discs is still warm
A brand new, sweet vinyl disc!
but not yet hard. It still is warm, and would keep this bended shape if I'd keep it a while
Here the covers are printed
here all elements come together
the pressing has been done, but packaging needs to happen
here is the final checkpoint if all is right for packaging
you may take it out if you will!
these kind of discs we produce 5 to 6 times a year, that continues to sell, world wide
Here is the stock, in clean air, 18°celcius
Discs can be stored here in perfect condition
Packaging !
Bob Dylan
And in a bit of time I will 'lay' here, with 25.000 boxes of the Bach partitas !
And we can't sleep from 500 discs we're about to produce...
yeah! Well this is 40à 50.000 discs. Several times a year, same disc
From every disc we produce, we'll have several checks
The discs are being listened to full, a 100%
Also the labels are checked
If the guys here give green light to audio, label, cover, title, content, ...
then the pressing starts
While pressing, we still have two rooms for constant checks
One checks press 1-16, the other press 17-32
The entire day, these people take samples to check
So to guarantee the highest level of the complete production
Is there something, the presses stop and we fix the issue
-------------------------------------------
Police advisory group will add voices - Duration: 2:19.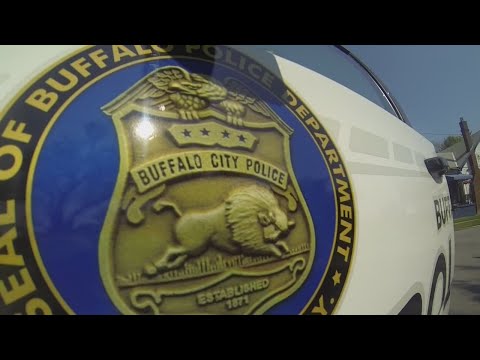
-------------------------------------------
Senator Bob Corker Will Not Seek Re-Election Next Year - Duration: 3:06.
-------------------------------------------
英國大學開學新生迎新活動 ft. Moose 英國留學香港仔 【Will Walker / 英國留學生活】 - Duration: 8:19.
-------------------------------------------
"The City Will be Overthrown" (5) - The Religious Babylon Is Destined to Fall Under God's Wrath - Duration: 19:39.
The religious world wildly resists and condemns Almighty God.
All their evil behavior has turned them into a bastion of antichrists.
Yes. It's true.
How ever could the religious Babylon the great not be destroyed by God? (Amen!)
It's just as Almighty God says,
Amen!
It should now be clear that
the religious community's history of resisting God
goes back at least to the end of the Age of Law.
Right. Yes.
When God was incarnated the first time and worked in the Age of Grace,
the religious world had already been controlled by antichrists and Pharisees,
and was opposed to the Lord Jesus' work of redemption. (Yes.)
When Almighty God, Christ of the last days, appears and does His work,
they continue to oppose God's judgment work in the last days.
Not only do they blaspheme against Almighty God,
they work with the CCP satanic regime to suppress the Church of Almighty God.
Once more, they have committed the heinous sin of recrucifying God!
Amen!
Not only did the Lord Jesus curse the Pharisees,
revealing the religious community's darkness,
but when Almighty God does judgment work of the last days,
He exposed the pastors' and elders' true essence: their resistance to God.
Yes. That's right.
In addition,
He cursed all the antichrists that once again crucified God on the cross.
Amen.
This is quite thought-provoking!
Yes.
When God was incarnated both times,
He cursed the religious community.
What does this show us?
God's elect at last grasps
that the religious community, Babylon the great, is indeed destined to fall.
Amen!
The religious community just believes in God in name
but doesn't exalt or bear witness to God.
They surely don't implement His will.
They cannot bring God's elect before His throne.
They surely can't lead them down the right path
so they understand truth and know God by practicing His words.
The religious leaders all completely go against God's will.
They don't practice the truth themselves,
but preach biblical knowledge and theological theory
to make people look up to and worship them.
Yes. That's right.
This all is the truth.
In reality,
they lead the believers on the hypocritical path of the Pharisees.
They hurt and they ruin God's elect.
And so, the religious leaders have all become the tools of Satan
and have become genuine antichrists.
Amen!
We had no idea what they were up to! (Awful!)
We were blind! (Yes.)
In the three stages of His work to save mankind,
God's been incarnated twice to redeem humanity and to save humanity.
The whole religious community is Christ's enemy.
They have become stumbling blocks to God's work of salvation.
They have offended God's disposition
and been punished and cursed by Him as a result.
Amen!
That is exactly what they deserved!
This really is just punishment for their sins!
It's just as the prophecies say,
Amen!
It's true. The religious community is Babylon! (Yes!)
We must quickly leave the religious community,
or we too will be punished by God!
Yes. We must stop being deceived and controlled by pastors and elders.
We won't let ourselves be destroyed as well! (Exactly!)
We must quickly leave, or we'll be punished by God as well!
Brothers and sisters,
the religious world wildly resists and condemns Almighty God.
All their evil behavior has turned them into a bastion of antichrists.
Yes. It's true.
How ever could the religious Babylon the great not be destroyed by God? (Amen!)
God's almightiness, righteous disposition, and wisdom
will be revealed when He destroys the satanic evil forces in the last days.
Amen!
After the great disasters, God will publicly reveal Himself!
Amen! Thanks be to God!
Thank God! (Yes, thank God!)
Brothers and sisters,
those who don't accept Almighty God's work of judgment in the last days,
no matter how they keep the Lord Jesus' name in the religious community,
no matter how they follow the Bible or religious ceremonies,
or even the salvation of the cross,
no matter how they labor, suffer or sacrifice,
if they don't repent and turn to Almighty God,
they'll be destroyed right along with the rest of the religious community.
Yes! That's right.
It was long ago that God ordained this; no one is able to change it!
Amen!
God called His elect back in the prophecies of Revelation,
Amen! Thanks be to God!
God called us long ago!
Thank God. Yes, yes, He did.
Brothers and sisters,
let's look at how Almighty God condemns these evil satanic antichrists
that fanatically resist God,
and the religious community that's controlled by antichrists.
Alright. Yes.
Amen!
Amen! Thanks be to God.
Sister Ma, when's Pastor Huang coming?
I've already sent him a text.
Amen!
God's words have so much authority!
Every sentence shall be fulfilled!
Brothers and sisters,
each of Almighty God's words is the truth;
they have authority and they have power;
they all display God's righteous, majestic,
wrathful, and unoffendable disposition. (Amen!)
Those who resist God, interrupt or disturb the work of God
will all receive God's retribution and punishment.
Amen!
In the Age of Law,
the citizens of Sodom publicly resisted and denied God.
They enraged His disposition
and so were all destroyed by God and reduced to nothing. (Yeah.)
In the Age of Grace,
the Jewish chief priests, scribes, and Pharisees
publicly resisted and condemned the Lord Jesus.
They worked with the Roman government to crucify the Lord Jesus upon the cross.
It was a grave sin that provoked God's disposition. (Yes.)
Yes. That's right.
The entire Jewish nation suffered unprecedented destruction.
Yes!
During the last days,
religious leaders wantonly condemn, resist, and judge Almighty God.
They even collude with the CCP devil
to suppress, arrest, and persecute those who spread the gospel of the kingdom.
Yes, it's true. Indeed.
Long ago they committed the heinous sins
of blaspheming against the Holy Spirit and recrucifying God.
Yes. They did.
Their behavior is even worse than that of Sodom.
Their evil behavior is even worse than that of the Jewish Pharisees. (Amen!)
Clearly,
they're the antichrists exposed by the work of God during the last days.
Yes. Indeed. They are. It's true.
They are the evil religious force
that has defied God fanatically than any other in history!
Yes. Right.
The religious community is entirely composed of evil forces that resist God.
It's a nest of antichrist demons.
Amen!
It is a staunch bastion
that tries to stand against Christ's kingdom as an enemy. (Amen!)
They are a satanic camp of sworn enemies to God that resisted Him! (Amen!)
God's righteous disposition can't be offended.
God's holiness can't be besmirched!
Amen!
The work of God in the last days
is the start of a new age and the end of an old age. (Yes!)
The religious community that is controlled by antichrist demons
as well as this whole evil world
will be destroyed soon by God's disasters within the last days.
Amen!
God's righteous punishment has already arrived! (Amen!)
It's just as Almighty God says,
look at page 317,
Amen!
Thanks be to God!
-------------------------------------------
God Will Appear Before You - Duration: 9:05.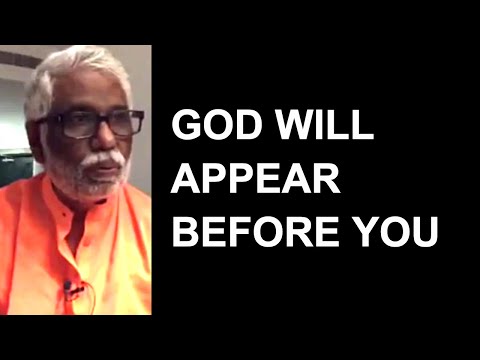
My video got disconnected.
It got disconnected for some reason because I didn't do it but God did it.
Because I was blah, blah blahing for seven minutes.
He said, "Say things precisely."
Which is, "God will appear before you."
Until that happens, nothing is going to happen.
You aren't going to stop your breath because you will die if you stop your breath.
And that is impossible and to turn the body into Light is even harder than that.
Stopping the breath should proceed before the body turning into the light.
(Speaks in Tamil) This is Manickavasar.
And he said, "I saw him with my eyes."
"He was like a Red Lotus Color, shining like millions of sun together."
"And I saw him.
Then he just this placed his foot on my head and I was done."
"I had an altered consciousness and in this consciousness, I lost my rational mind."
"But I was in bliss."
And that was an initiation.
And during Ramalingam's life, what happened.
Shiva appeared many times and then, as a Light Being, hugged him, and then the brain started
to function in a very different way.
And then, this has been the way that most people got enlightenment.
People who talk about enlightenment belong to a certain other category; and then they
die.
And I'm not here to talk about them, because that is not my model.
Or at least, I cannot relate to that model.
What I can relate to the model is a model of living a divine life, the life Divine.
And it cannot happen until you are blessed with it.
Sri Aurobindo meditated all his life, you know.
Getting into Pondicherry and meditating four months in a row and coming out and giving
a little bit of Darshan and going back into meditation again.
But he ended up getting old and blind.
So he didn't have the Grace.
So, the Grace -- This is the Mountain of Grace.
I have no doubt about it.
So I want to spend as much of my life here at this place going forward.
And that again, cannot happen until He permits me.
And then blesses me with that.
This is the best thing that has ever happened in my life.
And then, I am going to share with you many videos and also especially for those who have
been studying with me in the one-year program.
I have taken you through Three or four years of instructions.
And now, what I am going to talk about will completely take you to a different realm.
Because that is that is how it is, because learning on this earth plane, you don't find
anything instantaneously.
Time has to pass before we improve upon everything.
That's the nature of the earth plane.
So, you have to start with a 286 computer.
I don't know of anybody of many people will know what is a 286 computer to a cell, to
a mobile phone that acts like a computer today.
It's a matter of 40 years of time or more have gone since we have come to this point.
But at least we're happy.
So, what has to happen is -- God has to appear in front of you.
And that is going to be the videos that I would be doing.
And how that can happen.
And how it's comparable to other traditions where it is called some sort of an abduction.
You are abducted into a Light or taken into a different realm and changed.
And one thing that I remember, I think I've mentioned it before; Reagan was going for
his birthday party.
This is Shirley MacLaine who talks about it in her website.
And he was stopped by an Alien and then, said "What are you doing here?
You have to become the president of the United States."
And so he was delayed and delayed and delayed; and then he has to come and apologize to Shirley
MaClaine who organized this event.
"See, this is what happened to me."
And there's a book called "Reagan's God."
And then, you know, I can understand that book now after getting this information.
Who is an alien?
Alien is a God.
He is a God.
And this Harvard psychiatrist who wrote the book, "Passport to the Cosmos", I forget his
name now.
He was a great friend of Shirley MacLaine.
He was into that - into getting into a technology that can give us answers for our suffering.
We are all sufferering.
You may you may think that a billion dollar will give you liberation.
No -- it can give you a good hotel room.
And then, maybe some good wine and then you know, sex or what-not.
But then that's not going to give you God.
A billion dollar will never give you God.
So, you know, what is worthwhile is -- being in the company of God is trillion dollar worth.
You cannot put a value to that.
Because you'll be completely blissed out because you will realize your own identity is God.
So you know, when you listen to me, this particular video is very different from other videos.
Because I am speaking out from my own heart.
Of what all this is about.
And why are we, you know, like involved in the mad rat, in the rat race.
You know, to get money and then get old and die.
So that has to stop.
And then people have to really know what is life.
Stop it.
Stop it and do something about your own self realization.
-------------------------------------------
Karriere-Aus wegen Baby? Kylie Jenner will kürzer treten! - Duration: 1:37.
-------------------------------------------
Tesla Model 3 Will Cost $900 per Month - New Survey of 100K - Duration: 3:45.
-------------------------------------------
If You Blow Thumb, Here's The Effect it Will Have on Your Body - Duration: 4:29.
OUR WEBSITE : http://justhealthrelated.com/
If You Blow Thumb, Here's The Effect it Will Have on Your Body
If You Blow Thumb, Here's The Effect it Will Have on Your Body
The human organism works under, still to us, mysterious circumstances and even medicine
is shocked when something miraculous happens, proving that the body is more than able to
heal itself.
The stimulation of certain body parts can be successful for ameliorating the wellbeing
of other body parts.
In such way, one is able to fix various health problems, such as stress, pain, soreness and
more.
Sore throat fix
Although a cup of tea can work wonders, there are other ways that can also stimulate health
in the area.
Scratchy throat is a condition known and familiar to many, and it can sometimes become even
unbearable if left untreated.
Now, Scott Schaffer, M.D. President of an ear, nose and throat specialty center offered
a solution that many will find useful in this case.
As Dr. Schaffer put it, the most effective thing you can do is to scratch your ear!
"When the nerves in the ear are stimulated, it creates a reflex in the throat that can
cause a muscle spasm.
This spasm relieves the tickle," he noted.
Relax the nervous system
To get rid of stress and feel calmer, the only thing you need to do is to wash your
face with ice-cold water, while holding your breath.
This way, the water coldness will cause the "mammalian diving reflex."
What happens is, the organism is able to handle oxygen in a better way, which results in a
more relaxed organism.
Treating stress with cold water has been a home treatment known and practiced for years
in many cultures.
For a similar experience, you can simply drink an ice-cold glass of water.
This will help you relax even when splashing water on your face is off the table.
Beat the fear of needles
Injection treatment is never pleasant to anyone, so to deal with it more easily, all you need
to do is cough a little just before the needle touches your skin.
However, it is wise to talk the nurse into your practice, so things don't go south.
Stuffy nose rinse
This annoying little occurrence can truly be a thorn in your eye, but there is a way
to get rid of it easily.
All you need to do is press your tongue against the roof of your mouth, while pressing your
eyebrows by using the index fingers.
This technique will relax the nasal pathways, making it simple for you to dispose of the
nasal mucus.
While practicing this acupressure method, you need to breathe deeply every 20 seconds.
Treat burns
The first thing we do when getting burned is grabbing the ice pack and applying it on
the skin.
However, if you just use the tips of your fingers to press the burnt area, you will
get faster and more soothing results.
How that works is, it gives the affected area its normal temperature back while preventing
blistering at the same time.
Also, you won't be seeing any burn scars, which is amazing!
Deal with toothaches
One of the worst pains a person could experience is a sudden and uncontrollable toothache.
To get this under control, you need to apply an ice pack on the back of your hand.
Start rubbing the ice front and back along the skin between your index finger and thumb.
This is amazingly effective because the area has a lot of nerves directly connected to
the face and brain.
By icing the spot, you relieve the pain and send the brain signals to relax.
Calm your nerves
There is a simple hack on how to tone down those jumpy nerves and anxieties in your gut.
Just blow on your thumb!
As weird as it may sound, this method actually eases the breathing and soothes the Vagus
nerve, which is responsible for your heartbeat escalations.
No more migraines
Painkillers are such an old method to get rid of persistent headaches and migraines.
Instead, you can massage the area between your thumb and index finger with your other
thumb and forefinger.
Be gentle during the massage and proceed with it for two minutes before switching on to
the other hand.
To get the best results, apply pressure in circular movement.
This enables the blood flow to run faster and releases the Ki energy throughout the
body.
Don't Forget To Follow Us On Other Social Media :
INSTAGRAM: http://bit.ly/2m7bnd1 FACEBOOK: http://bit.ly/2kYKuD0
TWITTER: http://bit.ly/2l74mVA PINTEREST: http://bit.ly/2lEUYvn
Subscribe our channel for more!
-------------------------------------------
WHY A POTENTIAL CONFLICT BETWEEN US AND NORTH KOREA WILL BE VERY SHORT ? - Duration: 7:44.
North Korea's foreign minister has accused US President Donald Trump of declaring war
on his country and said Pyongyang had the right to shoot down US bombers.
Ri Yong-ho said this could apply even if the warplanes were not in North Korea's airspace.
The White House dismissed the statement as "absurd".
The Pentagon warned Pyongyang to stop provocations.
A UN spokesman said fiery talk could lead to fatal misunderstandings.
In this video, Defense Updates analyzes WHY A POTENTIAL CONFLICT BETWEEN US AND NORTH
KOREA WILL BE VERY SHORT UNLIKE THE CASE IN VIETNAM, IRAQ OR AFGHANISTAN?
Lets get started.
North Korea is known to possess chemical weapons (CW).
While assessing CW stockpiles and capabilities are difficult, the DPRK is thought to be among
the world's largest possessors of chemical weapons, ranking third after the United States
and Russia.
In 2012, the South Korean Ministry of National Defense estimated that the DPRK possesses
between 2,500 and 5,000 metric tons of chemical weapons.
In particular, it has a large supply of VX nerve agent, last year it was used to assassinate
Kim Jong Un's half-brother, Kim Jong Nam, at Kuala Lumpur airport.
VX is considered to be one of the most toxic chemical weapons ever produced, even a "microscopic
amount" can prove deadly
At maximum capacity, North Korea is estimated to be capable of producing up to 12,000 tons of CW.
Nerve agents such as Sarin and VX are thought be to be the focus of North Korean production.
North Korea is believed to be capable of deploying its stockpile of chemical agents through a
variety of means, including field artillery, multiple rocket launchers, FROG rockets, Scud
and Nodong missiles, aircraft and unconventional means.
Additionally, U.S. military authorities believe there is long-range artillery deployed in
the DMZ, along with ballistic missiles capable of delivering chemical warfare agents.
In Vietnam, Iraq or in Afghanistan the adversary didn't have such lethal chemical weapons
and US did not posses the current crop of highly accurate tactical nukes.
This situation will warrant the use of lethal force with possible use of tactical nuclear weapons.
While North Korea's massive forces are largely primitively equipped, Pyongyang possesses
the capacity to launch a devastating artillery strike on the city of Seoul.
The opponents' capitals are just 120 miles apart, with Seoul within 35 miles of the border.
Most of the North's artillery pieces—numbering in the thousands—are already in place camouflaged
and dug in.
North Korea's artillery pieces include the 170 mm Koksan, which has a range of about
25 miles (40 km), using conventional projectiles.
However, the Seoul is well within range of the Korean People's Army rocket-assisted
shells—which have a range of around 40 miles (60 km), if the guns are stationed near the
border region.
Being self-propelled, 170 mm Koksan can be easily moved close to the international border.
Covering only about 12% of the country's area, the Seoul Capital Area is home to more than
48.2% of the national population, and is the world's third largest urban area.
An artillery barrage will result in huge civilian casualty apart from loss in property and destruction
of infrastructure.
This scenario will again force US to use military option that can subdue the North Korean forces
quickly, and this is potentially possible with use of tactical nukes.
North Korea tested intercontinental ballistic missile (ICBM) named HWASONG-14 on that has
the range to hit major US cities.
North Korea has tested this ICBM twice in July and both times the test was successful,
marking a major milestone for the country.
This is the first time North Korea has demonstrated the capability to strike US homeland.
A missile is as destructive as its warhead, which is why North Korea is running missiles
and nuke program in parallel.
In total North Korea has conducted 6 nuclear tests till now.
The first nuke test was conducted by North Korea on Oct. 8, 2006.
As per the United States analysts, it had a yield of less than one kiloton of TNT.
Blasts have become more powerful since then.
The device tested by the North recently had a yield of more than 100 kilo tons of TNT.
In case of a conflict, US has no option but to take out the North Korean nukes and missile sites.
This is only possible with the use of lethal force, which includes precision bombs as well
as tactical nukes to destroy hardened underground storage facilities.
The crux of the matter is that unlike Vietnam, Iraq or Afghanistan, a war with North Korean
will be a race against time.
Giving North Korean chance to retaliate will result in catastrophe.
Traditional warfare methodology with boots on the ground will not be an apt option.
Keeping this in view US will have to bring in the big weapons from the very beginning
including possible use of tactical nukes.
The war will be swift and will be fought at lightning pace.
US cache of tactical nukes has the potential to shorten the war like what happened in World
War 2.
B61 nuke is one of the weapons that can play a major role.
B61 is a variable yield, kiloton-range weapon.
Tactical versions can be set to 0.3, 1.5, 5, 10, 45, 60, 80, or 170 kiloton explosive
yield and the strategic version has a yield 340 kilotons.
Trump's words, threatening to meet North Korea's threats with a "fire and fury like the world
has never seen" were the starkest warning of a nuclear strike from any U.S. president
in modern times.
Also Trump in UN speech said, referring to the regime of North Korean leader Kim Jong
Un :
"No nation on Earth has an interest in seeing this band of criminals arm itself with nuclear
weapons and missiles.
The United States has great strength and patience, but if it is forced to defend itself or its
allies, we will have no choice but to totally destroy North Korea."
The tone and language does indicate that Trump administration is open to using nukes.
Không có nhận xét nào:
Đăng nhận xét